Look up details on regional product approvals and how Therma-Tru products meet these standards.
PrismaGuard Testing
Tested to meet tough expectations.
PrismaGuard premium finish is put through multiple rigorous tests in our engineering labs. This helps ensure that our PrismaGuard finish is built to last, just like the Therma-Tru® doors it was designed for.
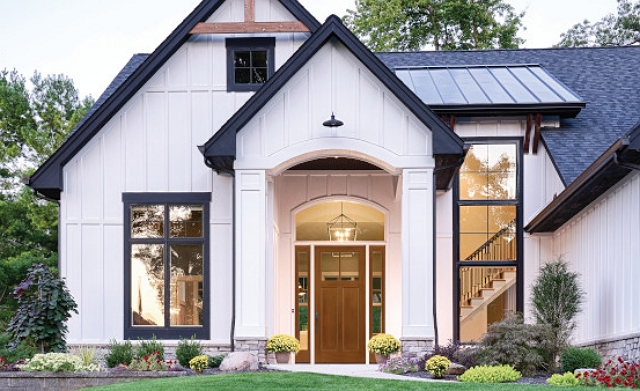
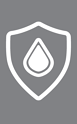
Lasting beauty and color.
Using specialized equipment, PrismaGuard stains and paints are tested to help deliver a consistent high-end appearance perfect for wood-grained or smooth door surfaces.
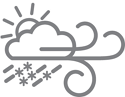
Protection from the elements.
Therma-Tru simulates exposure to harsh environments to help verify that PrismaGuard finish coating protects the door from the elements, preserving its color for years to come.
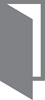
Resistance against wear and tear.
PrismaGuard finish is subjected to a simulation of everyday use to provide a durable high-end, low-maintenance finish that protects the door from normal wear and tear.
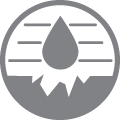
Confidence on the coast.
Therma-Tru simulates a highly corrosive atmosphere to help ensure PrismaGuard finish can withstand the damaging effects of high-salt environments near the coast.
Tested for lasting beauty.
Therma-Tru uses specialized testing equipment on PrismaGuard stains and paints to help deliver a consistent high-end appearance perfect for wood-grained or smooth door surfaces.
- The specular gloss test (ASTM D0523) measures the reflection of light off the finish at an exact angle to help ensure the finished door’s flawless appearance and added dimension.
- The color difference test (ASTM E1347, ASTM E308, ASTM D2244) establishes color standards for comparison to help verify that the finish preserves the door’s color over time.
- The viscosity measurement test (ASTM D4212) measures the finish to a controlled thickness that allows for even application of the handcrafted finish by the professionals who perfect it.
Resistance against wear and tear.
Therma-Tru subjects PrismaGuard finish to simulated everyday use to provide a durable high-end, low-maintenance finish that protects the door from normal wear and tear.
- The tape adhesion test (ASTM D3359) applies pressure sensitive tape to the finished surface and pulls it away to help verify the finish will not peel or rub off the door.
- The conical mandrel bend test (ASTM D522) bends the finished surface around a controlled spinning object to help confirm its flexibility to resist cracking and surface damage.
- The abrasion resistance test (ASTM D4060) rubs the finished surface against a weighted abrasive wheel to help ensure that the finish can resist scraping from normal use.
- The pencil hardness test (ASTM D3363, ISO 1518-1) drags pencil leads of varying hardness across the finished surface at a specified angle to help confirm it can resist scratches.
- The chemical resistance test (AAMA 605) exposes the finished surface to common chemicals to help ensure it can withstand the chemicals used in home construction and household cleaning.
- The Gardner impact strength test (ASTM D2794) drops a specific weight on the finished surface from a set distance to help confirm that the finish can resist damage from impact.
Protection from the elements.
Therma-Tru simulates exposure to harsh environments to help verify that PrismaGuard finish coating protects the door from the elements, preserving its color for years to come.
- The extreme weathering tests (ASTM D6695, ASTM G151, ASTM G154, ASTM G155) place finish samples in accelerated weather chambers that recreate cycles of intense sunlight, humidity, heat and water spray to help ensure that the finish can resist color fading and other defects caused by exposure to the elements over time.
- The 100% relative humidity test (ASTM D2247) exposes finish samples to high-moisture conditions to help ensure the finished door can resist damage due to high humidity.
Confidence on the coast.
Therma-Tru simulates a highly corrosive atmosphere to help ensure PrismaGuard finish can withstand the damaging effects of high-salt environments near the coast.
- The salt fog immersion test (ASTM B117) immerses finish samples in a simulated saltwater fog to help verify that the finished door resists damage from exposure.